The oil and gas industry is changing. It’s facing many challenges for efficiency improvements and cutting costs. AI in oil and gas equipment manufacturing addresses these challenges. It is reshaping equipment manufacturing.
This article shows how AI is making these changes. It also explains how computer vision and machine vision help streamline work. AI in oil and gas equipment manufacturing makes processes smoother, boosts performance, and ensures quality results. It does this using computer vision and machine learning.
Key Takeaways:
- Predictive Maintenance: AI finds problems early. This keeps equipment running longer and reduces disruptions.
- Digital Twin Optimization: Digital twins test drilling setups virtually. This saves money by avoiding physical prototypes.
- Real-Time Inspections: AI finds equipment flaws in real time. It catches errors that humans might miss, improving accuracy.
- CNC Machinery: AI in oil and gas equipment manufacturing meets special needs like unique rigs and valves. This meets companies’ specific needs for unique rigs, specific valves, and other things.
- Corrosion Control: AI manages anti-corrosion coatings for uniform application. This improves protection and reduces recoating needs.
Predictive Maintenance in Oil and Gas Equipment Manufacturing
AI-driven predictive maintenance is crucial for oil and gas equipment manufacturing. It detects early signs of failure, ensuring fewer disruptions. By predicting problems early, AI uses resources better and extends equipment life.
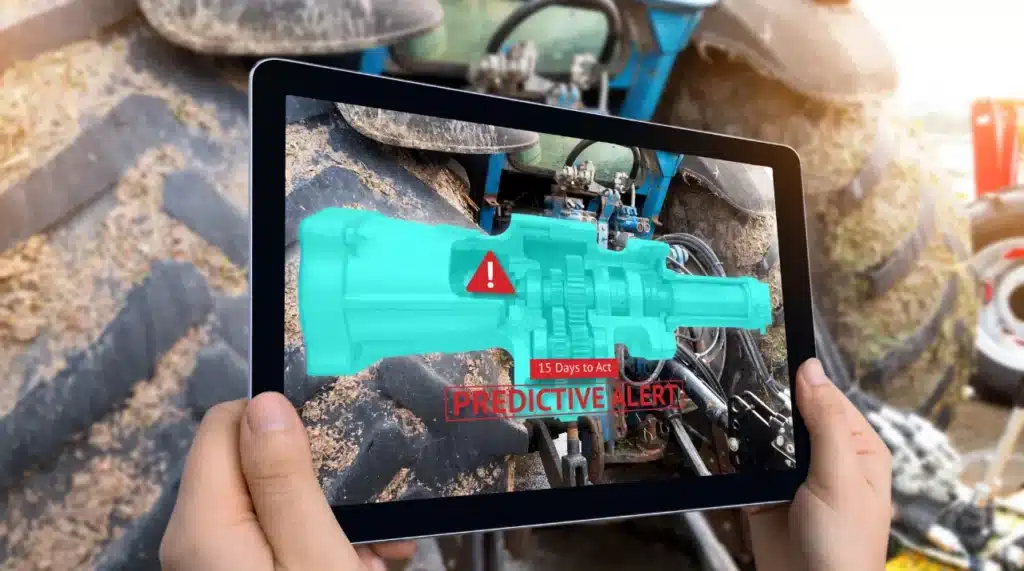
Specific Cases
AI-based predictive maintenance makes equipment more reliable and efficient. It works well with machines like water injection pumps, compressors, and turbines. Sensors gather data on these machines. AI predicts failures and sets maintenance schedules. This reduces maintenance needs, extends equipment life, and cuts downtime.
Maintaining subsea equipment is costly because of harsh environments. AI predicts failures in critical systems, like blowout preventers. This allows operators to act before big issues happen. AI sensors watch conditions and flag problems right away. This proactive monitoring keeps things running smoothly.
Quality Control with AI
Enhanced Welding Quality with AI and Laser Scanning
AI with laser scanners watches welding in real time. It finds problems to keep weld quality high. This makes pipelines, rigs, and infrastructure stronger. AI improves welding quality and infrastructure stability.
AI-powered vision inspects parts in real time. It finds flaws that humans might miss. Machine vision makes sure only quality parts move forward. AI helps keep quality high in oil and gas manufacturing. This reduces waste and boosts accuracy. AI in oil and gas equipment manufacturing ensures quality control by catching flaws missed by humans.
AI-driven computer vision measures equipment dimensions. It checks if components like valves, pumps, and pipes meet standards. It also finds defects like tiny cracks and welding issues. This keeps equipment reliable in tough conditions.
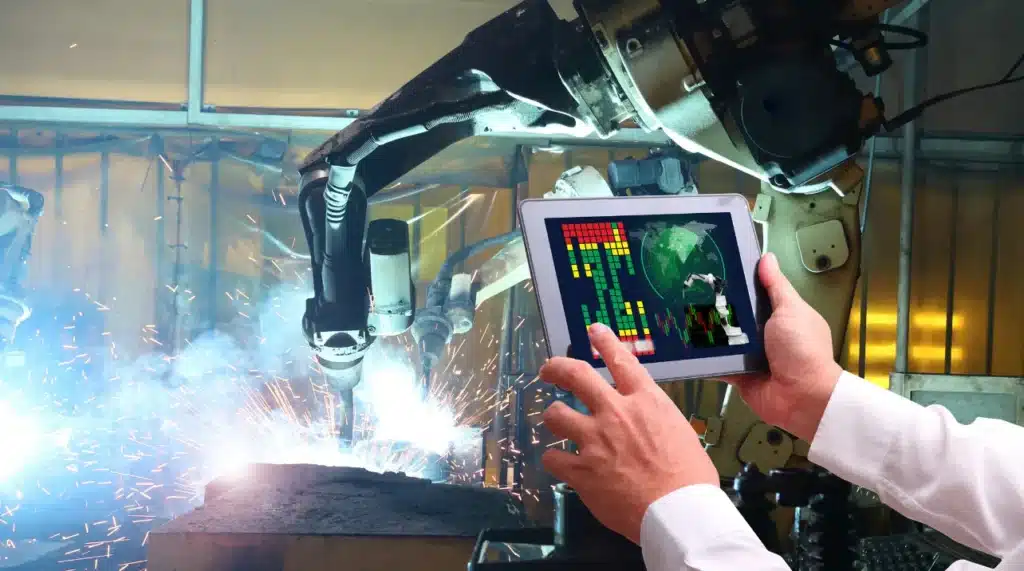
AI in Surface Treatment Processes
AI controls spray parameters for anti-corrosion coatings. It makes sure the coating is applied evenly. This boosts protection and reduces the need for re-coating.
Digital Twin Design Optimization
Digital twins are virtual models of products. Manufacturers use them to test changes before equipment production. This cuts risks and saves money. Another study tested digital twins in conjunction with PdM techniques to have an active approach for preventing faults in machine tools.
Digital twins help create complex equipment efficiently. For example, they simulate oil drilling setups. This improves designs without physical prototypes. The result is cost savings and better performance.
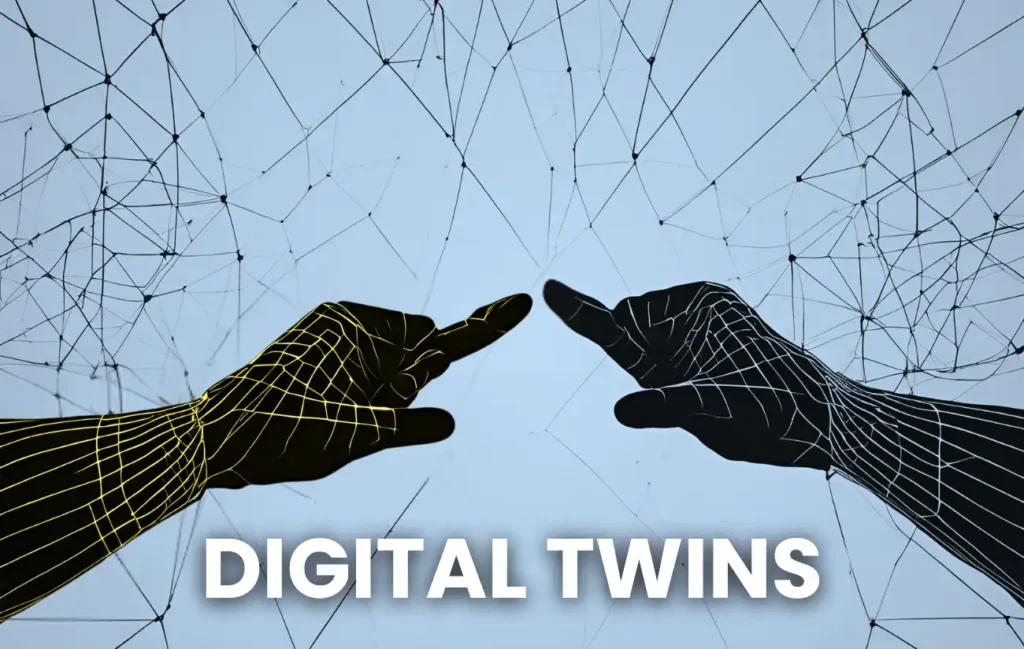
AI and Worker Safety
AI boosts production and safety. It predicts hazards like overheating or pressure changes. AI in oil and gas equipment manufacturing allows quick action in response to hazards.
AI also uses robots for unsafe tasks. This helps keep workers safe. Robots can enter small spaces and handle high heat. They inspect pipelines and automate valve checks, which makes operations safer.
The Impact of AI on Cost Reduction in Equipment Manufacturing
AI cuts costs in equipment manufacturing. It helps optimize raw materials and reduces unnecessary expenses. AI predicts material needs, which helps avoid waste. Another benefit is for greater machine performance.
AI in oil and gas equipment manufacturing helps reduce idle time. It helps with rapid prototyping using digital simulations. This shortens production time, reduces waste, and boosts efficiency.
Energy Consumption and Sustainability
AI reduces energy use by analyzing patterns. By analyzing patterns, AI in oil and gas equipment manufacturing finds areas for improvement, and helps make the process become more sustainable.
Customization Abilities with AI in Oil and Gas Equipment Manufacturing
AI works with CNC machinery to make custom parts. This ensures components meet unique needs. Companies need special parts like custom rigs, pipelines, and valves. AI uses customer data to adjust production. This allows tailored manufacturing and increases satisfaction.
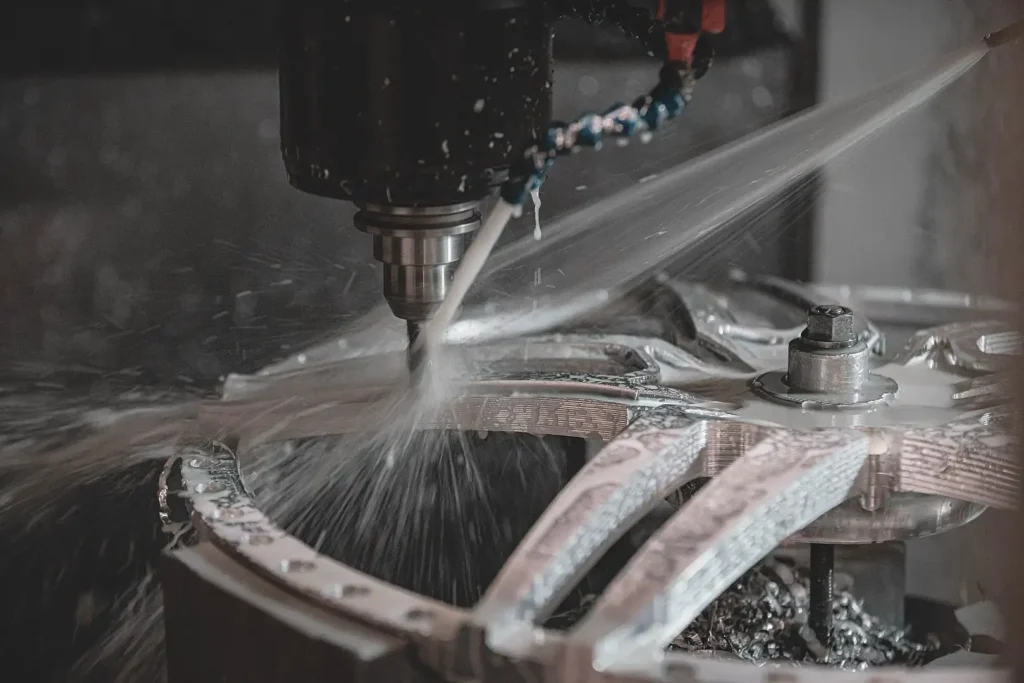
Challenges of Implementing AI
AI has many benefits but also some challenges. Implementing AI needs investment in tech and training. Some companies hesitate because of the cost. Data quality is also an issue. AI needs lots of good data. The problem is good data can be hard to acquire in these working conditions. This leads to inefficient or bad data.
Bad data therefore leads to wrong predictions and costly mistakes. Oil and gas equipment is often in remote places like offshore rigs. This makes data collection hard. One research paper goes into more detail, regarding this challenge. Despite these challenges, the long-term benefits make it worth the costs.
Future of AI in Oil and Gas Equipment Manufacturing
AI will play an even bigger role in the future. As technology advances, AI will be more affordable. The industry will use AI more for automation. AI will keep improving efficiency, cutting costs, and making operations safer. Companies that use AI early will gain big advantages.
AI-driven predictive maintenance will keep evolving. It will focus more on upstream operations. AI will continue boosting efficiency and reliability. It will also help lower maintenance costs. This is crucial for expensive industries like oil and gas.
Conclusion
In conclusion, AI in oil and gas equipment manufacturing is a game changer. It drives efficiency. It improves quality, worker safety, and customization. AI for predictive maintenance reduces downtime and keeps equipment running smoothly. Digital twins, machine vision, and real-time monitoring help optimize processes.
They also cut costs and improve performance. Companies that use AI in oil and gas equipment manufacturing will be more productive and profitable. The industry is ready for big changes, and AI will be at the center of these advancements, making operations smarter and stronger.
Want Flawless Product Quality?
Book a free strategy call to see how AI-powered inspection can streamline your production.
Gediminas Mickus
Business Development Manager