Quality inspection of plastic bags is a critical step in manufacturing processes where defects such as sealing inconsistencies, cracks, and unmelted particles can compromise product integrity.
Traditional manual inspection methods are labor-intensive, inconsistent, and prone to human error, leading to inefficiencies and quality issues.
To address these challenges, an advanced computer vision-based inspection system was implemented to enhance accuracy, efficiency, and scalability.
The Challenge
Plastic bag manufacturers face several challenges in ensuring consistent quality standards:
- Manual Inspection Limitations:
Manual quality checks require significant time and effort and often lead to inconsistent results due to operator fatigue and subjective judgment. Minor defects such as unmelted particles or micro-cracks can go unnoticed, impacting product reliability. - Seal Integrity Detection:
One of the most critical aspects of plastic bag production is ensuring strong and uniform seals. Traditional inspection methods struggle to detect minor variations in seal quality, resulting in undetected weak points that can compromise the bag’s functionality. - Surface Defect Detection:
Identifying surface defects such as cracks, contamination, or foreign particles presents a challenge due to variations in material transparency and texture. Standard inspection techniques often fail to capture subtle defects, leading to costly quality control issues.
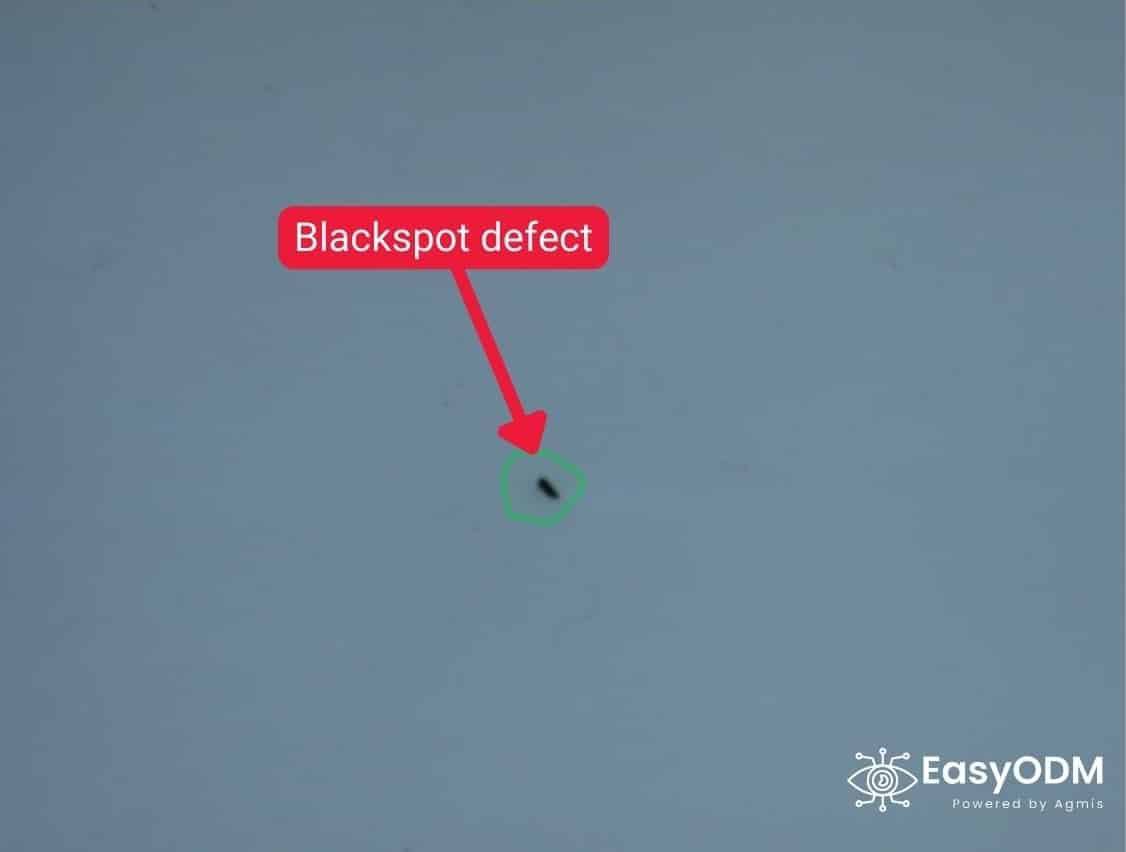
Defects Detectable in Plastic Bag Production
Through the implementation of a computer vision system, the following defects can now be accurately detected:
- Holes in the bag: Small punctures or tears that compromise the integrity of the packaging.
- Gland breakage: Structural breakages in the sealing area, potentially leading to leaks.
- Leakage between bag layers: May occur due to overheated seams or misaligned film layers.
- Incorrect sealing location: Unintended heat seals outside the designated sealing areas.
- Burnt/unmelted raw material granules: Contamination due to processing errors, affecting product quality.
- Insects: Presence of foreign contaminants trapped inside the packaging.
- Tiny holes near gland seam: Small perforations in the seam that could lead to leaks.
- Incomplete seam sealing: Areas where the seam is not fully bonded, risking product containment failure.
- Gland seam stretching: Excess tension causing deformation or thinning of the seam.
- Wrinkles/channels: Irregularities in the film layers that may weaken the bag structure.
- Layer adhesion: Undesirable sticking of layers, leading to difficulties in opening the bag.
- Damaged gland: Mechanical damage affecting the seal integrity.
- Sealed cutout: Incorrectly fused cutout sections that impact the bag’s usability.
- Particle trapped under Teflon: Contaminants trapped during sealing, causing structural weaknesses.
The Solution
To overcome these challenges, a computer vision system was deployed, incorporating advanced imaging hardware and AI-powered algorithms to provide automated, high-precision defect detection.
1. Optimized Inspection Setup
A robust inspection system was implemented with the following key components:
- Industrial Camera:
Capable of capturing high-resolution images with optimized exposure settings to highlight defects with minimal noise. - Lighting Solutions:
Multiple lighting configurations, including white backlights and polarizing filters, were tested to ensure even illumination and eliminate reflections for maximum defect visibility. - Automation Integration:
Encoder-based synchronization was introduced to capture images with precise timing, enabling seamless integration into high-speed production lines.

2. Advanced Defect Detection Techniques
The solution involved a hybrid approach, leveraging both traditional image processing and machine learning algorithms for defect detection.
- Seal Integrity Analysis:
The inspection system utilizes rule-based algorithms to straighten and segment seal regions, followed by AI-based classification to detect inconsistencies such as incomplete seals and weak bonding areas. - Surface Defect Detection:
Machine learning models trained on thousands of samples were used to identify cracks, unmelted plastic particles, and foreign objects. Images were tiled into smaller patches to improve detection accuracy in high-resolution scans. - Defect Visualization:
Heatmaps and overlay visualization techniques were incorporated to highlight detected defects, allowing operators to verify results and improve decision-making in quality control processes.
Results Achieved
By implementing the computer vision system, the following key improvements were achieved:
- 99% Accuracy in detecting unmelted plastic particles in clear plastic bags.
- 97% Accuracy in identifying cracks and seal defects.
- 99% Accuracy for foreign objects in clear bags.
- 50% Reduction in overall inspection time compared to manual processes.

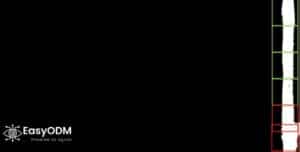
Expert Conclusion and Analysis
The integration of computer vision for plastic bag inspection represents a significant leap forward in manufacturing quality assurance. This case demonstrates how a combination of precision imaging, tailored lighting solutions, and AI-driven defect detection can overcome longstanding challenges in quality control, providing a scalable and reliable solution for high-volume production environments.
The deployment of high-resolution industrial cameras, combined with optimized lighting configurations such as white backlighting and polarizing filters, has proven effective in eliminating common inspection challenges such as glare and uneven illumination. This foundational setup ensures that defects—whether related to seal integrity or surface inconsistencies—are captured with high contrast and clarity, allowing the machine learning models to operate with maximum efficiency.
The achieved 99% accuracy in detecting unmelted plastic particles and 97% accuracy in identifying cracks and seal defects highlight the system’s ability to identify even the most subtle quality issues that manual inspections often miss. This level of precision is essential for maintaining product integrity and regulatory compliance in industries where quality standards are non-negotiable.
From an operational standpoint, the system’s ability to reduce inspection time by 50%, while maintaining a false positive rate below 5%, underscores the practical benefits of transitioning from manual to automated inspection. Not only does this reduce the dependency on human labor, but it also ensures consistency and repeatability in defect detection, ultimately leading to lower production costs and higher customer satisfaction.
Furthermore, the adoption of AI-based defect classification offers manufacturers an adaptive quality control approach. As the system continues to learn from new data, it becomes more proficient at recognizing evolving defect patterns, ensuring long-term reliability and continuous improvement.
In conclusion, this case study serves as a testament to the transformative potential of computer vision in industrial applications. With the right combination of imaging technology, AI algorithms, and process optimization, manufacturers can achieve unprecedented levels of quality assurance, streamline operations, and enhance their competitive edge in the market.
For manufacturers seeking to modernize their quality control processes, investing in computer vision technology is no longer just an option—it is an essential step toward operational excellence and future-proofing production lines.
Want Flawless Product Quality?
Book a free strategy call to see how AI-powered inspection can streamline your production.
Gediminas Mickus
Business Development Manager