The quality inspection of car seats presents numerous challenges, including the testing of electrically or optically indistinguishable features, the monitoring and documentation of test parameters, the physical strain on testing personnel, and a reduction in the availability of qualified staff.
To address these challenges, the integration of robot automation into the test system is proposed, along with the use of optical measurement systems. This approach not only enhances the quality and efficiency of production but also ensures compliance with safety standards.
Accurate position determination in automation processes is crucial to prevent rework, longer cycle times, and damage to test specimens or production components.
Various techniques for position determination, such as precise positioning on workpiece carriers, force-guided approaches, tactile measurement using force sensors, and optical measurement using camera systems, are explored in this article.
By establishing boundary conditions and reducing tolerances, the overall quality inspection process of car seats can be significantly improved and the overall production ROI improved.
Key Takeaways
- Machine learning and advanced image recognition techniques can accurately classify indistinguishable features in car seat quality inspection, enhancing efficiency and accuracy.
- Monitoring and documenting test parameters in real-time allows for immediate detection of deviations or anomalies, providing valuable insights for continuous improvement.
- Ergonomic design of workstations and tools, as well as automation of repetitive tasks, can reduce physical strain on testing personnel and improve efficiency and accuracy.
- Robotic arm integration and optical measurement systems offer benefits such as improved accuracy, reliability, and throughput, but require careful planning, execution, and technical expertise to overcome challenges and optimize their capabilities.
Testing Electrically/Optically Indistinguishable Features
Testing electrically/optically indistinguishable features, like patterns in the seat fabric, particular shapes or textures, or electrical components that look alike, poses a significant challenge in car seat quality inspection.
It requires accurate methods to differentiate and assess these features. Traditional inspection techniques may struggle to effectively identify and evaluate these features, leading to potential quality issues.
However, advancements in machine learning applications and advanced image recognition techniques offer promising solutions to address this challenge.
By leveraging machine learning algorithms and sophisticated image analysis algorithms, it is possible to train computer systems to accurately identify and classify these indistinguishable features.
Integration of automation solutions like EasyODM, which leverages advanced image recognition techniques and machine learning algorithms, offers a promising solution.
EasyODM can be trained to accurately identify and classify these indistinguishable features, significantly enhancing the efficiency and accuracy of car seat quality inspection. You can read the full case study here.
These techniques can greatly enhance the efficiency and accuracy of car seat quality inspection, ensuring that all features are properly assessed and meet the required standards.
By incorporating machine learning applications and advanced image recognition techniques, car seat manufacturers can improve their quality control processes and deliver products of the highest quality.
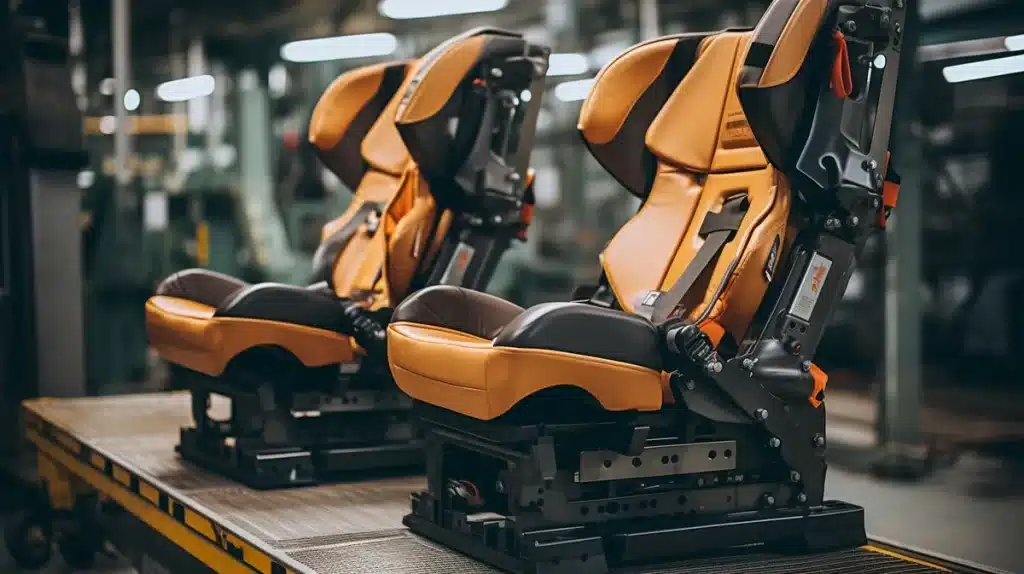
Monitoring and Documenting Test Parameters
Monitoring and documenting test parameters requires meticulous attention to detail and accurate record-keeping throughout the entire testing process.
In the context of car seat quality inspection, this task is of utmost importance in ensuring the reliability and validity of the test results.
Real-time monitoring of test parameters allows for immediate detection of any deviations or anomalies that may affect the quality of the car seats.
This enables timely corrective actions to be taken, minimizing the impact on production efficiency and overall product quality.
Additionally, data analysis of the monitored parameters provides valuable insights into the performance of the testing process, allowing for continuous improvement and optimization.
Physical Strain on Testing Personnel
The physical strain experienced by individuals involved in the testing process poses a significant concern in ensuring the overall efficiency and accuracy of car seat quality inspection.
This strain can lead to fatigue, decreased focus, and potential errors in the testing process. To address this issue, physical strain reduction techniques and automation benefits can be employed.
- Ergonomic design: Implementing ergonomic workstations and tools can reduce strain on testing personnel, allowing them to perform tasks more comfortably and efficiently.
- Automation of repetitive tasks: By automating repetitive tasks, such as lifting heavy objects or conducting repetitive movements, the physical strain on testing personnel can be significantly reduced.
- Robotic an AI assistance: Integrating AI robotic systems into the testing process can further reduce the physical strain on testing personnel by performing tasks that require heavy lifting or precise movements. This allows personnel to focus on more complex and critical aspects of the inspection process.
Reduction in Availability of Qualified Staff
One of the concerns in the car seat quality inspection process is the limited availability of personnel with the necessary qualifications and expertise.
This reduction in the availability of qualified staff poses a challenge for ensuring the highest quality standards in car seat production.
To address this issue, companies can consider strategies such as retraining and upskilling their existing workforce or outsourcing and hiring new personnel with the required skills.
Also, EasyODM machine vision software offers a solution by providing consistent and reliable defect recognition without the need for extensive training or expertise.
Its user-friendly interface ensures that both existing and new personnel can effectively utilize the software, minimizing the impact of staff shortages on inspection quality.
In order to provide a comprehensive understanding of the current situation, the table below highlights the advantages and disadvantages of each approach:
Approach | Advantages | Disadvantages |
---|---|---|
Retraining and upskilling | – Utilizes existing workforce | – Time-consuming process |
– Cost-effective solution | – May require additional resources for training | |
– Builds loyalty and motivation among employees | – Some employees may not have the aptitude for training | |
Outsourcing and hiring | – Access to specialized expertise | – Increased costs |
– Potential for faster recruitment process | – Integration challenges | |
– Allows for flexibility in staffing | – Cultural fit issues |
Ensuring Highest Quality Standards
To ensure the highest quality standards, it is essential to implement robust quality control measures throughout the car seat production process.
This includes the use of automation techniques to improve efficiency and accuracy in quality inspection. However, there are implementation challenges that need to be addressed.
- Integration of automation systems: The successful implementation of automation techniques requires the seamless integration of robotic arms and optical measurement systems into the existing test system. This requires careful planning and coordination to ensure compatibility and functionality.
- Compliance with safety standards: Automation in car seat testing should not compromise the safety of personnel or the integrity of the test specimens. It is crucial to comply with safety standards and regulations to prevent accidents or injuries.
- Overcoming technical limitations: Automation may face challenges in accurately determining the position of features on the car seats. Precise position determination is essential for quality inspection. Overcoming technical limitations and ensuring accurate position determination is crucial for maintaining the highest quality standards.

Increased Quality and Efficiency in Production
Increased quality and efficiency can be achieved in the production of car seats through the implementation of automation techniques.
By integrating robotic arms into the testing system and using optical measurement systems, the production process becomes more streamlined and accurate. This not only ensures compliance with safety standards but also prevents accidents or injuries.
Moreover, automation techniques allow for precise position determination, which is crucial in maintaining the highest quality standards. Incorrect position determination can lead to increased rework, longer cycle times, and damage to the test specimen, resulting in unusable components in the production process.
Techniques such as precise positioning, force-guided approaches, tactile measurement, and optical measurement can be employed to accurately determine the position of car seat features.
Overall, the implementation of automation techniques in car seat production enhances productivity and leads to significant cost savings.
Increased Productivity | Cost Savings |
---|---|
Streamlined production process | Reduction in labor costs |
Improved accuracy and reliability | Minimization of rework and wastage |
Enhanced throughput and cycle times | Optimization of resources |
Prevention of errors and defects | Reduction in inspection and maintenance costs |
Higher output with consistent quality | Maximization of overall efficiency |
Integration of Robotic Arm Into Test System
The integration of a robotic arm into the test system allows for enhanced precision and efficiency in the position determination of car seat features.
This integration, however, presents certain challenges that need to be addressed. One such challenge is ensuring seamless integration of the robotic arm into the existing test system. This involves compatibility issues, software integration, and communication protocols.
Another challenge is optimizing the robotic arm capabilities to accurately position the car seat features. This requires advanced algorithms and control systems to achieve the desired level of precision.
Lastly, the integration process needs to be carefully planned and executed to minimize disruptions and downtime in the production process.
Overall, overcoming these integration challenges and harnessing the full potential of robotic arm capabilities can greatly enhance the accuracy and efficiency of car seat quality inspection.
Use of Optical Measurement Systems
Optical measurement systems offer a non-contact method for accurately determining the position of car seat features, thereby improving the precision and efficiency of quality inspection processes. These systems have several advantages in car seat quality inspection.
Firstly, they provide a non-destructive and non-invasive approach, eliminating the need for physical contact with the seat. This reduces the risk of damage to the seat during the inspection process.
Additionally, optical measurement systems can capture detailed and high-resolution images of the seat features, allowing for thorough analysis and measurement. Moreover, these systems can quickly and accurately measure multiple features simultaneously, saving time and increasing productivity.
However, there are also challenges in implementing optical measurement systems in car seat quality inspection. These include the need for proper calibration and alignment of the system, ensuring adequate lighting conditions for accurate measurements, and addressing potential issues related to reflections and surface properties of the seat material.
Overcoming these challenges requires careful planning, technical expertise, and continuous optimization of the measurement system.
Compliance With Safety Standards
Adherence to safety standards is a critical requirement in the implementation of measurement systems for car seat quality inspection. Safety compliance challenges arise in the automation of car seat testing processes.
To ensure safety, the following precautions should be taken:
- Implementation of safety protocols and guidelines to prevent accidents or injuries during the testing process.
- Regular maintenance and inspection of the automated systems to ensure they are functioning properly and do not pose any safety risks.
- Training of personnel on safety procedures and protocols to minimize risks and ensure their well-being.
Prevention of Accidents or Injuries
In the context of car seat quality inspection, preventing accidents or injuries and ensuring worker safety is of paramount importance.
Automation solutions play a crucial role in achieving these objectives. By replacing manual labor with robotic systems, the physical strain on testing personnel can be significantly reduced.
Additionally, the integration of robotic arms into the test system allows for increased quality and efficiency in production.
To comply with safety standards, optical measurement systems can be employed to accurately monitor and document test parameters without the need for direct human involvement.
By eliminating the risk of human error and reducing the reliance on qualified staff, automation solutions not only improve the overall quality of car seat testing but also create a safer working environment.
Preventing Accidents or Injuries | Ensuring Worker Safety | Importance of Automation |
---|---|---|
Reduced physical strain | Compliance with safety standards | Improved quality and efficiency |
Elimination of human error | Safer working environment | Reduction in reliance on qualified staff |
Improved monitoring and documentation | ||
Prevention of accidents or injuries |
Conclusion
The challenges in car seat quality inspection are significant, ranging from the testing of electrically or optically indistinguishable features to the physical strain on testing personnel and the reduction in the availability of qualified staff.
However, solutions are at hand. Automation, particularly through the integration of robotic arms and optical measurement systems, offers a promising way forward.
Machine vision and advanced image recognition techniques can effectively classify indistinguishable features, enhancing efficiency and accuracy.
Real-time monitoring and documentation of test parameters enable immediate detection of deviations, facilitating continuous improvement. To alleviate the physical strain on testing personnel, ergonomic design and automation of repetitive tasks are key strategies.
Addressing the shortage of qualified staff requires thoughtful approaches like retraining and upskilling or outsourcing specialized expertise. To ensure the highest quality standards, safety compliance, and overcoming technical limitations are paramount.
By embracing automation, car seat manufacturers can achieve increased quality and efficiency, streamline production, reduce errors, and enhance worker safety.
The integration of robotic arms and optical measurement systems represents a path towards meeting these challenges head-on and delivering car seats of the highest quality.