Plywood manufacturing is changing. This change is driven by new technology. One key advancement is AI in plywood quality control. AI now helps ensure consistent quality.
It detects defects, helps reduce waste, as well as improves production efficiency. In this article, we explore how AI is reshaping plywood production, focusing on its benefits, uses, and challenges.
Key Takeaways
- Automated Defect Patching: AI can use advanced spraying systems for defect repair. This ensures precision and reduces manual labor.
- Precision in Putty Application: AI in plywood quality control applies the exact amount of putty needed. This prevents waste and cuts costs.
- Real-Time Glue Line Inspection: AI inspects glue lines for issues. This improves plywood strength and cuts defects.
- Adaptive Learning: AI learns from past inspections to improve. It adapts to new defects fast.
- Consistency Across Batches: AI inspects without fatigue. This consistency helps make high-quality plywood.
The Role of AI in Plywood Quality Control
AI is starting to lead in many industries. Plywood production is no exception. Quality control used to depend on human inspectors. They looked for flaws like cracks or uneven surfaces. This was slow and prone to mistakes. It also relied on the skill of the inspector. Now, AI is changing quality control.
AI systems use cameras and sensors to collect data. Advanced algorithms then process this data. These algorithms can spot defects better than human eyes. AI in plywood quality control also makes inspections faster. This means better quality control. AI can inspect thousands of sheets in the time it takes a human to check one.
How AI Enhances Plywood Quality
AI Detection of Surface Defects
AI in plywood quality control works in stages. AI in plywood quality control uses machine learning models to spot patterns that point to flaws. For example, they can find discoloration or grain issues.
Learning from Past Inspections
AI systems can learn from past mistakes. The more they inspect, the better they get. This is a big advantage over traditional methods. AI can learn to spot new defect types. It can adapt faster to changing production needs.
Automated Defect Identification
Recent research shows that AI systems can find plywood related defects with great accuracy. Cameras or laser scanners collect surface data, which is then processed. Algorithms like Support Vector Machines (SVM) and Artificial Neural Networks (ANN) greatly increase accuracy in defect detection.
Automated Defect Patching
The automated patching system uses collected data to make repair decisions. A specialized sprayer then applies putty to the defects. The exact amount depends on the defect’s size and spot. This reduces labor costs and keeps quality consistent. AI in plywood quality control also speeds up the process.

Predictive Quality Control
AI can predict adhesion quality during gluing. It looks at variables like adhesive amount, temperature, and timing. Machine learning models such as SVM and ANN help predict outcomes. This ensures each panel meets standards and reduces failures.
Improved Consistency
AI provides consistent quality checks without getting tired. It reduces the number of defective products compared to human inspection. Human inspectors can get tired or lose focus. AI does not have this issue. It offers consistent quality, sheet after sheet.
Speed and Efficiency
AI systems are quick. They can process large amounts of plywood in a short time. This means increased output. In turn, this boosts productivity and reduces downtime.
Enhanced Efficiency with Defect Patching
AI defect patching follows the best path for repairs. This cuts down on manual work. Precise spraying means fast and correct patching, which leads to greater production speed.
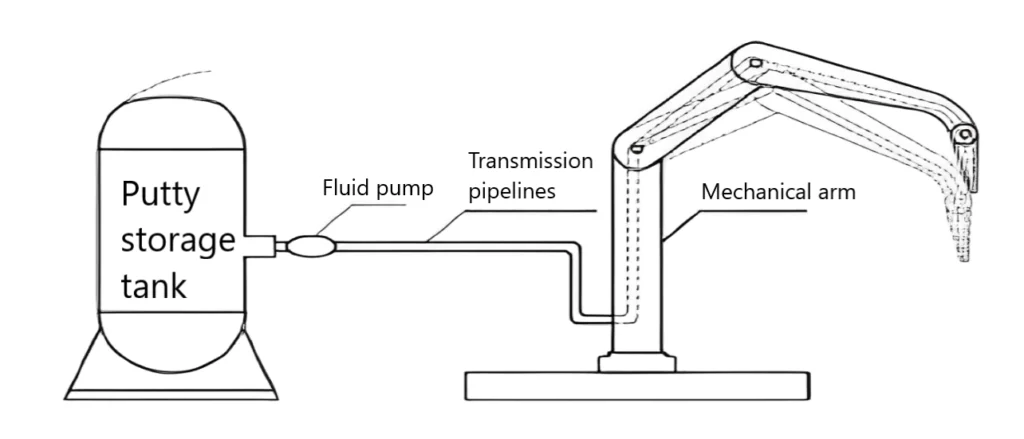
Cost Reduction
Research shows that automated defect patching saves costs. By controlling putty use and reducing labor, it lowers waste and extra costs. AI reduces waste by finding defects early. This stops flawed products from moving forward in the process. It saves materials and cuts down waste, leading to long-term savings.
Data Insights
AI does more than find flaws. It also collects data. Manufacturers can use this data to find trends in quality problems. These insights help improve production. They can also predict future issues.
AI systems that automate patching give insights into defect patterns. By studying these trends, manufacturers can change production steps to reduce defects. AI also learns continuously, improving defect detection and repair.
Applications of AI in Plywood Quality Control
Veneer Peeling and Glue Line Inspection
AI can be used at many stages of plywood production. One key use is during veneer peeling. The peeled veneers are checked for grain consistency. Any flaws are flagged. AI also helps inspect glue lines. Good adhesion is key to strong plywood. AI-based systems can find even tiny glue defects.
Final Product Inspection and Automated Patching
Another use is in final product inspection. AI in plywood quality control checks for cracks and voids that affect plywood strength. Machine learning methods, like KDD, help find these defects in real-time. This makes sure only quality plywood goes to customers.
AI systems also use automated patching for defects. Cameras or lasers detect flaws in real-time. Automated sprayers then apply the right amount of putty. This improves repair accuracy and quality.

EasyODM’s AI Solutions for Wood Quality Control
EasyODM offers AI-driven solutions tailored for wood industry’s quality control across different types of wood products. These solutions are highly customizable to meet the unique needs of each manufacturer.
By leveraging advanced machine vision software technology, EasyODM can detect a wide range of defects, such as cracks, chips, knots, and grain irregularities. This helps manufacturers maintain consistent quality, reduce waste, and enhance safety throughout the wood processing industry.
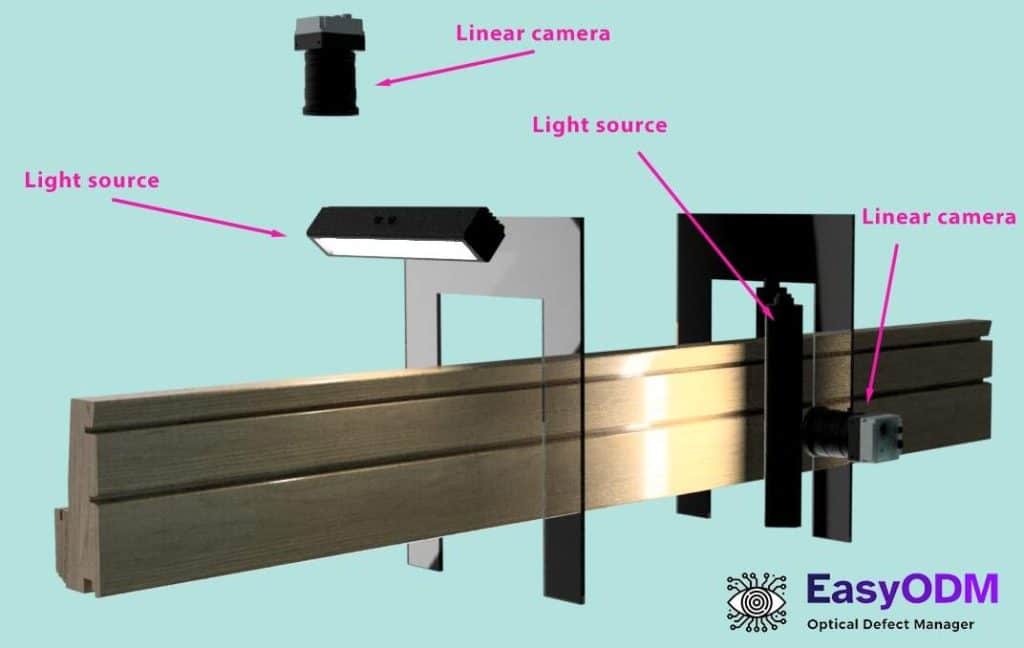

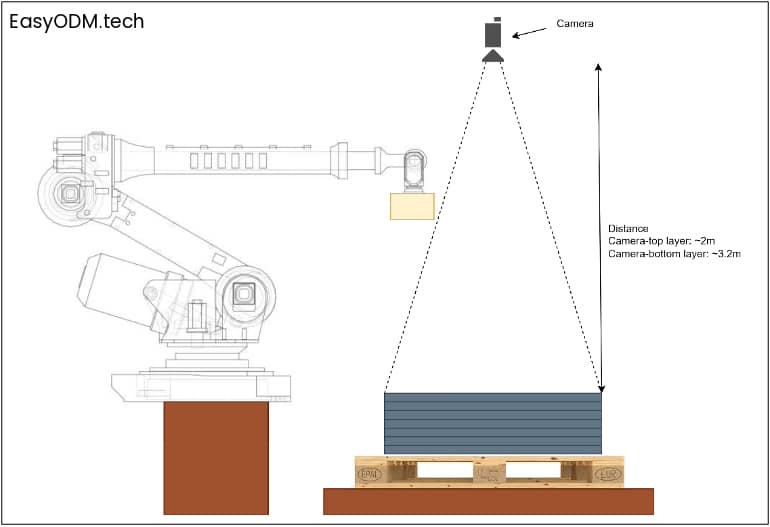
Challenges in Implementing AI
AI in plywood quality control has some challenges. The initial cost is high due to spending on hardware, software, and training. Although, long-term savings can make up for these costs.
AI systems also need skilled staff for maintenance. Poor data can lead to bad results. Good input data is key for good performance. For example, the AI-based patching system needs precise data from scanners. Inaccurate data can lead to mistakes. So, calibration and regular updates are crucial.
The Future of AI in Plywood Manufacturing
AI in plywood quality control will grow. As technology improves, AI will become easier to access. Better algorithms will give better quality control. Predictive maintenance advancements are also going to be developed further.
Conclusion
AI in plywood quality control is changing the industry. It adds consistency, speed, and accuracy to production. AI-based defect patching is a big step forward. It brings automated repair processes that improve quality control.
While there are challenges, the benefits are much greater. As AI grows, plywood production will keep improving. Adopting AI gives manufacturers an edge. For manufacturers, using AI is not just staying current—it is about staying competitive.
Want Flawless Product Quality?
Book a free strategy call to see how AI-powered inspection can streamline your production.
Gediminas Mickus
Business Development Manager